

The dotted lines indicate the core material losses, and at 1 MHz, the 3F3 material is a little superior to 3C90. But there isn’t a big difference between the two at 100 kHz, and they both have reasonable performance up towards 1 MHz. Both are 2000 times better than air, and that is important. This tells us how much better than fresh air they are at (a) concentrating the magnetic flux and (b) constraining it. At 100 kHz, they both have a value of around 2000. The solid lines show the material’s magnetic permeability (the ferrite “feel-good” factor). The first comparison is the frequency response, i.e., how high a frequency is the ferrite material suitable for: The next thing is to look into both these material types to see if one might be preferred over the other. The common material types are 3C90 and 3F3. The E38/8/25 core can be bought in several different ferrite materials.

Study and choose the ferrite material (stages 2 and 3) Hence, we have targeted a planar core-set. Another aim of this design is to keep the overall profile height as low as possible. On the right is how the core set and PCB will be constructed The copper PCB tracks will form the coil loops, and we may have to stack several small PCBs to get the right number of turns.
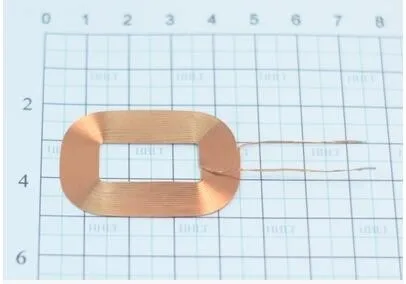
It is shown using the blue line in the figure below: It is the average travel distance of the magnetic flux when two core halves are brought together. Highlighted in the red box is the core’s effective length (ℓ e) this is an important value for calculating the peak flux density. The part number is E38/8/25, and two halves are needed to make a full core-set: The design we are using as the basis of this article is aiming for an inductance of about 1 mH, and the ferrite material that will be considered is a planar type made by Ferroxcube. Temperature drift causes inductance change and can alter how a tuned filter might perform.The upper operating frequency is limited due to other (eddy current) core losses.A magnetic flux density of 400 mT brings saturation losses. The magnetic field is constrained to the ferrite core, thus reducing interference with close-by components and circuits.The magnetic field is magnified, and we can make an inductor with fewer turns leading to reduced copper losses.

Make sure this is the best material for your application before proceeding.Īdvantages of using a ferrite core inductor The stages are as follows: Stage 1īefore proceeding, the implications of the decision to use ferrite cores rather than any other material needs to be considered. The process involves a sequence of steps requiring the use of several data sheets and, should the ferrite core inductor design need to be gapped, some degree of iteration. In this article, I’m going to take you through the standard ferrite cores selection guide and design process used in applications such as a DC-to-DC converter or a power filter inductor.
